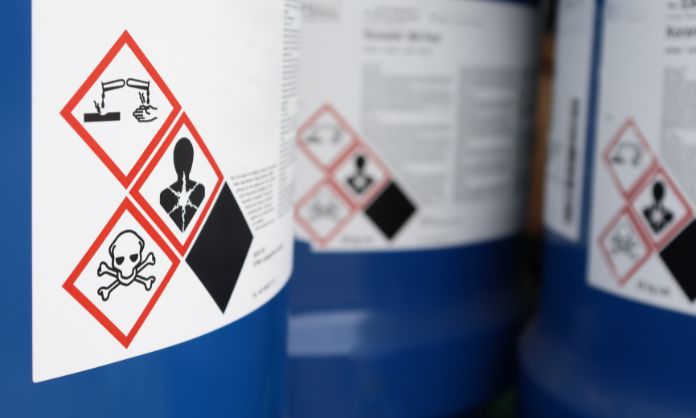
Workplace hazards pose a threat to the safety and well-being of employees. Employers, supervisors, and workers share the responsibility for minimizing risks through proactive measures, regular training, and adherence to safety regulations. Learn about the top safety hazards in the manufacturing industry, what causes them, and how to manage them.
Slips, Trips, and Falls
Slips, trips, and falls are some of the most prevalent workplace injuries. They can result from various factors, including cluttered workspaces, protruding objects, worn or uneven flooring, and poorly maintained walking or working surfaces.
Preventing these incidents requires a combination of proactive measures. Keeping hallways, aisles, and exits clear of items helps eliminate tripping hazards. Regularly inspecting and maintaining floors, platforms, ramps, stairs, and walkways can prevent slips and falls due to damaged or uneven surfaces. Training managers, supervisors, and workers on the importance of reporting and promptly cleaning up spills and other hazards can further reduce these risks.
Moving Machine Parts
Belts, gears, chains, and rollers, often referred to as moving parts of machinery, can cause significant harm if not handled safely.
Here are some specific hazards of moving machine parts:
- Entanglement: Clothing, hair, or body parts can become entangled in machinery, potentially leading to fractures, dislocations, or abrasive injuries.
- Crushing: Moving components can trap parts of the body, leading to crushing injuries.
- Cuts and abrasions: Sharp edges on gears or chains can cause cuts or abrasions.
- Struck-by injuries: If a belt, chain, or gear breaks, it can cause parts to be ejected from the machine, potentially striking workers.
These potential hazards highlight the importance of safety measures like using machine guards and personal protective equipment. Personnel must follow safety regulations, such as those created by OSHA, and the manufacturer’s directives to protect themselves from machinery.
Chemical Hazards
Mishandling chemicals is a top safety hazard in the manufacturing industry because toxic substances can result in burns, respiratory issues, and long-term health complications. Workers must review safety data sheets and hazardous material labels to handle and store chemicals properly. Additionally, employers must conduct training sessions to emphasize the seriousness of chemical hazards and instill best practices for managing them.
Proper chemical storage prevents chemical reactions that could lead to fires, explosions, or the release of toxic gases, which can harm people, property, and the environment. While various industries implement different hazmat storage solutions, they all start by accurately identifying and classifying their hazardous materials. This ensures that incompatible substances are stored separately to prevent dangerous reactions.
Following safety regulations and regular training can prevent harm from slips, trips, falls, moving machine components, and hazardous chemicals. A culture of safety protects workers and creates a more positive work environment, so ensure everyone in your facility understands your business’s pertinent safety protocols.